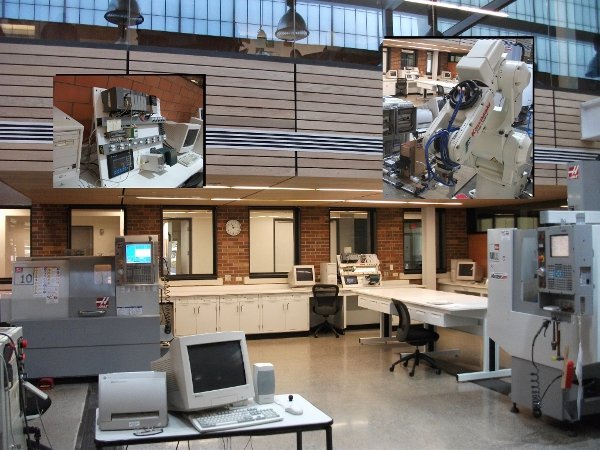
This lab houses the Kawasaki robot. It is a six degrees of freedom electric robot with a pneumatic gripper. It is used in a work cell built by some students used for a palletizing application. This work cell uses multiple sensors (inputs) and multiple outputs. They are all wired to the controller. There is also a teach pendant that is used for teaching of points. Students are taught how to program the robot using the AS language. (Unfortunately robot languages are not standardized and every robot uses a different language). They also learn about wiring the inputs and outputs to the controller. Students learn in other classes about the internal design of the robot. It consists of gears, motors and linkages.
In the demonstration shown the robot is used to palletize blocks that have been loaded in a hopper by a human. Blocks are pushed, drilled and clamped by pneumatic cylinders and an air motor. The robot will palletize the parts on a pallet that is at an angle compared to the robot. They have different reference frames. The program is completely flexible from the palletizing view point. We can specify the number of rows, columns and layers as we desire. The points are calculated from a long and relatively complicated program.
One can see also two computer numerical control (CNC) machines. The milling machine is used for flat parts, whereas the lathe is used for cylindrical stock. Students draw up parts using some type of drawing software, such as AutoCad or SolidWorks. The drawings are imported in the MasterCam software where the student selects the desired tool paths. The code is then post processed for the HAAS machine. The students then have to setup the machine after loading the work piece and the tools. Work offsets and tool length compensations have to be done. The machine is now ready to produce parts. The CNC mill has an automatic tool changer (ATC) for ten parts whereas the lathe has an ATC for 12 tools.
Programmable Logic (PLC) trainers with variable speed drives and human machine interfaces (HMI) are used for AC motor control. There are five Allen Bradley programmable logic controllers that can be used for programming of an AC motor using variable speed drives and a human machine interface. These PLCc and HMIs are also connected on a Ethernet network and can communicate with each other. A student at one station can control the motor at another station if the right communication program logic is also programmed in.
A fully automated can crusher using PLC control was built by students using pneumatics. The machine was entirely built from scrap material. It is actually used by the students to crush cans for the green project.